Hot Tanks
Full immersion cleaning
Whether it involves cleaning ferrous or non-ferrous components, the Apollo agitating heavy-duty hot tank equipment is capable of completing the most difficult of cleaning tasks
The patented centrifugal filter makes Apollo’s agitating Hot Tanks the world leader in this field. The centrifugal filter provides a major saving in chemical replacement due to the significant extension in the service life of the cleaning solution. With chemical savings of up to 92% and electricity savings over 25% you can potentially save hundreds of thousands of dollars over the whole-of- life ownership of the machine.
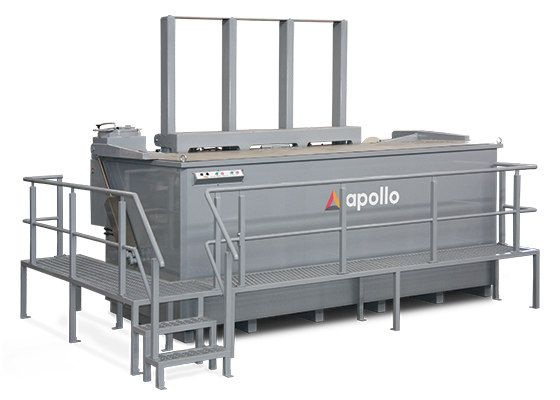
Simple, safe operation
& faster cleaning
Save over 75% on chemicals over the life of the machine
Save up to 25%
on electricity
Save man-hours
Increase workshop
productivity
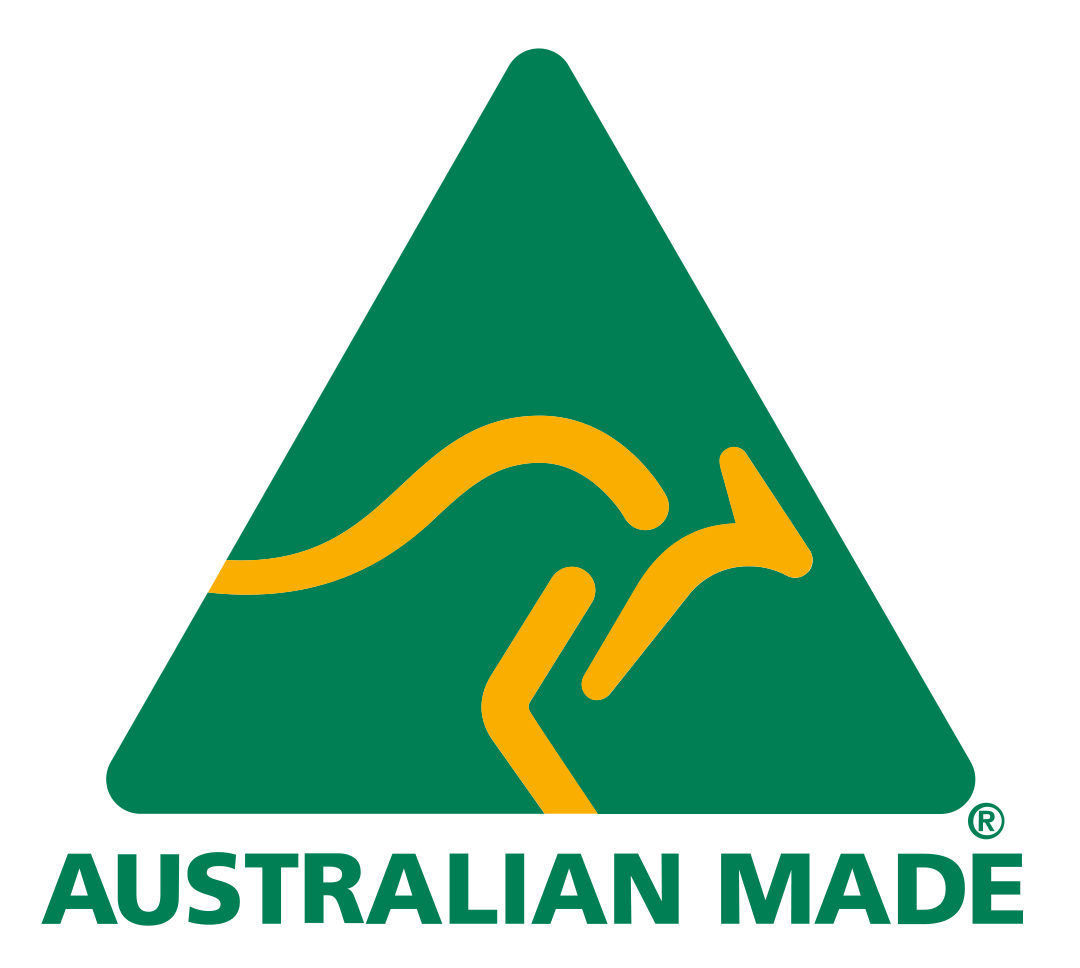
CUSTOMER REVIEWS
Powerful engine cleaning results
We recently introduced the new Apollo Cleaning chemicals (EziClean and EziBoost) into our existing Apollo Hot tank, and the results have been outstanding. The system delivers exceptional cleaning performance, removing carbon, rust, paint, grease, and oil from engine blocks. The time-saving efficiency and reduction in manual labour have significantly boosted our productivity.
Regards
Paul Bedford
Engine Reconditioning and Engineering
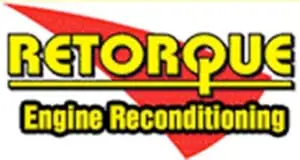
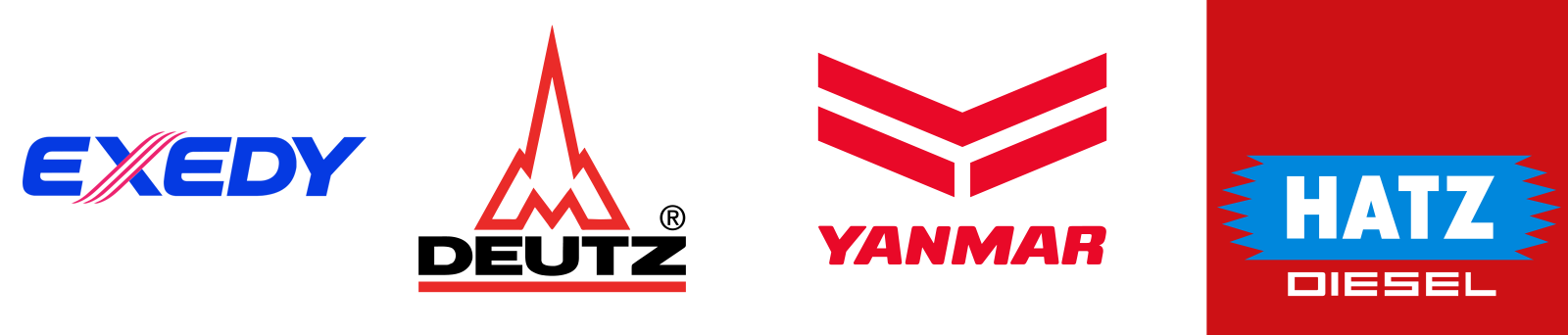
The visit from Apollo Engineering was incredibly beneficial for our team. They helped us get one of our tanks working properly and identified issues with another that would have otherwise gone unnoticed. The depth of knowledge and expertise from Toma and Scott was invaluable. Thanks to their insight, we now have a dedicated approach to operating and maintaining our equipment, which has already led to noticeable improvements. We truly appreciate Apollo’s support and professionalism.
John, Roma
Models Specs
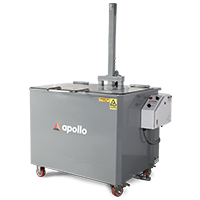
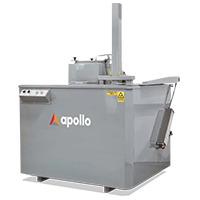
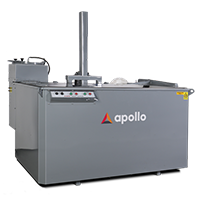
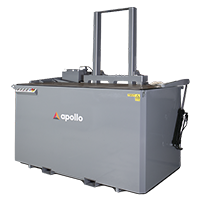
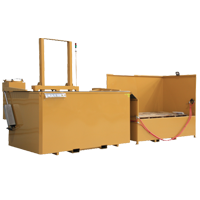
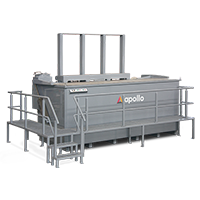
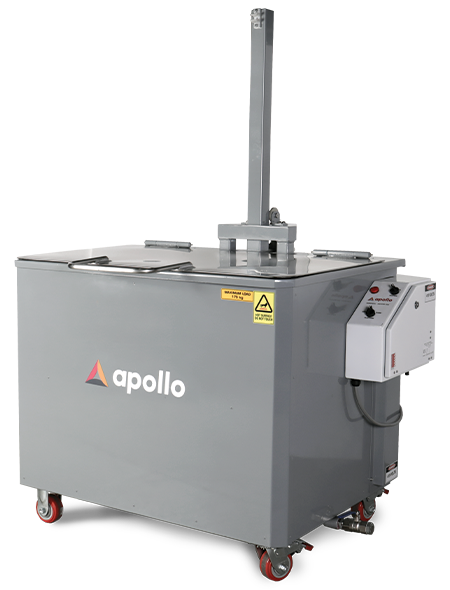
Specification | Details |
---|---|
Platform (L x Wmm) | 1000 x 600 |
Floor Space (L x Wmm) | 1260 x 1035 |
Working Depth (mm) | 600 |
Platform Raised (mm) | 860 |
Max. Load (kg) | 175 |
Power Required | 415V, 10A |
Element Size | 3 x 2.4kW |
Oil Skimmer | N/A |
Centrifugal Filter | N/A |
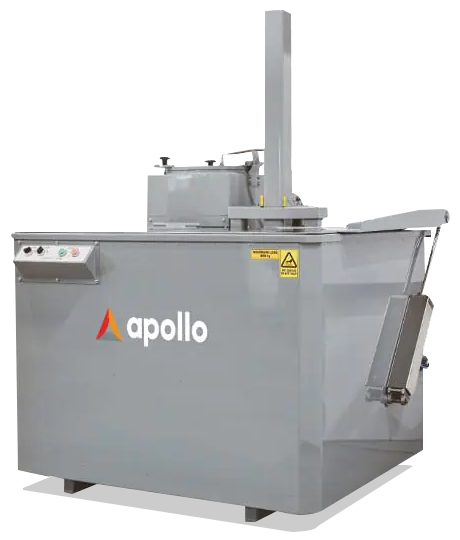
Specification | Details |
---|---|
Platform (L x Wmm) | 1210 x 780 |
Floor Space (L x Wmm) | 1450 x 1450 |
Working Depth (mm) | 600 |
Platform Raised (mm) | 1000 |
Max. Load (kg) | 400 |
Power Required | 415V, 20A |
Element Size | 3 x 3.6kW |
Oil Skimmer | N/A |
Centrifugal Filter | Standard* |
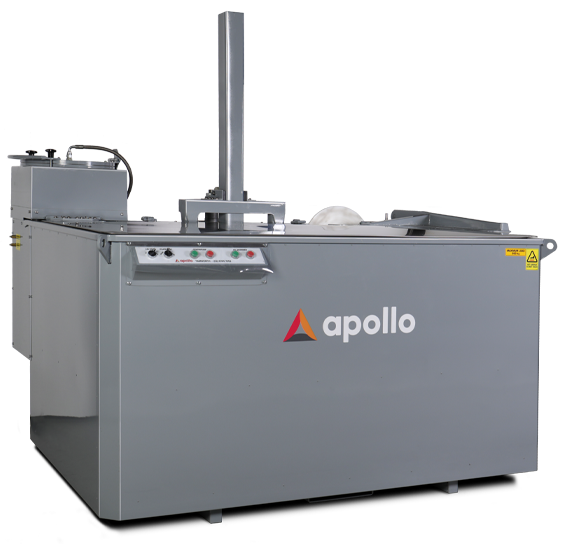
Specification | Details |
---|---|
Platform (L x Wmm) | 1860 x 930 |
Floor Space (L x Wmm) | 2200 x 1650 |
Working Depth (mm) | 700 |
Platform Raised (mm) | 1100 |
Max. Load (kg) | 900 |
Power Required | 415V, 32A |
Element Size | 3 x 6kW |
Oil Skimmer | Standard* |
Centrifugal Filter | Standard* |
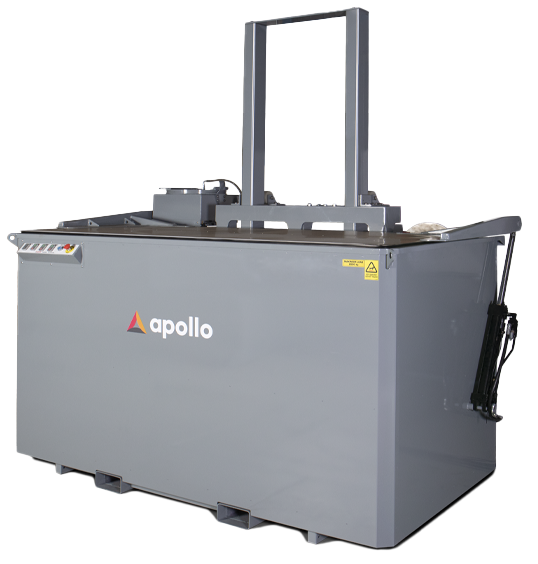
Specification | Details |
---|---|
Platform (L x Wmm) | 2400 x 1020 |
Floor Space (L x Wmm) | 3000 x 1870 |
Working Depth (mm) | 1050 |
Platform Raised (mm) | 1520 |
Max. Load (kg) | 2000 |
Power Required | 415V, 60A |
Element Size | 6 x 6kW |
Oil Skimmer | Standard* |
Centrifugal Filter | Standard* |
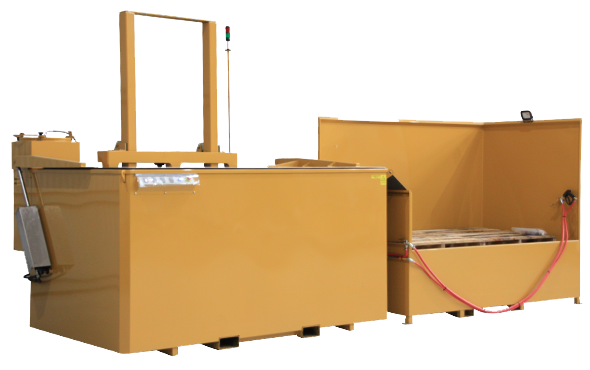
Specification | Details |
---|---|
Platform (L x Wmm) | 2660 x 1420 |
Floor Space (L x Wmm) | 3050 x 2320 |
Working Depth (mm) | 1050 |
Platform Raised (mm) | 1520 |
Max. Load (kg) | 2500 |
Power Required | 415V, 100A |
Element Size | 9 x 6kW |
Oil Skimmer | Standard* |
Centrifugal Filter | Standard* |
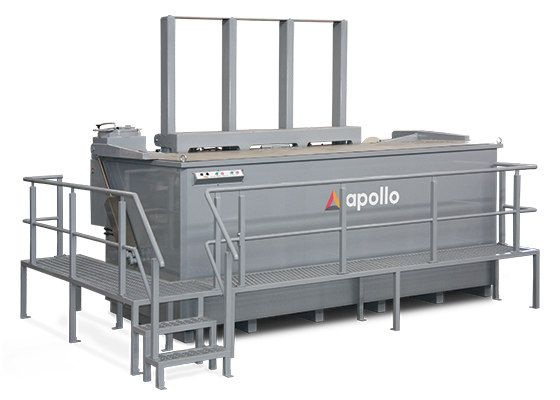
Specification | Details |
---|---|
Platform (L x Wmm) | 3720 x 1410 |
Floor Space (L x Wmm) | 4230 x 2440 |
Working Depth (mm) | 1080 |
Platform Raised (mm) | 1750 |
Max. Load (kg) | 4000 |
Power Required | 415V, 150A |
Element Size | 12 x 8kW |
Oil Skimmer | Standard* |
Centrifugal Filter | Standard* |
Case Studies
high-performance parts washers that deliver powerful and cost-effective cleaning solutions.
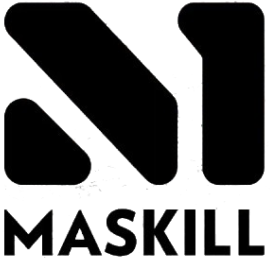
By automating our cleaning processes, we're saving hours per job!
– Casey Maskill,
Supply Manager

The team are very friendly, engaging and reliable and continue to assist in achieving desired outcomes that help our business grow.
– Don Pollard
Lead Designer/ Production Manager
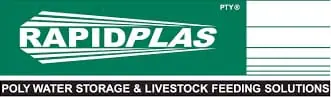
Apollo can complete any job we require and we are proud to have a local engineering company supporting our manufacturing efforts.
– Gavin Scott,
Research & Development
Difference Between Hot Tanks and Automated Spray Washers
A hot tank submerges parts for extended cleaning, ideal for baked-on contaminants, while an automated spray wash parts cleaner uses high-pressure jets to clean parts faster and with less manual effort. Spray washers are more efficient for frequent cleaning.
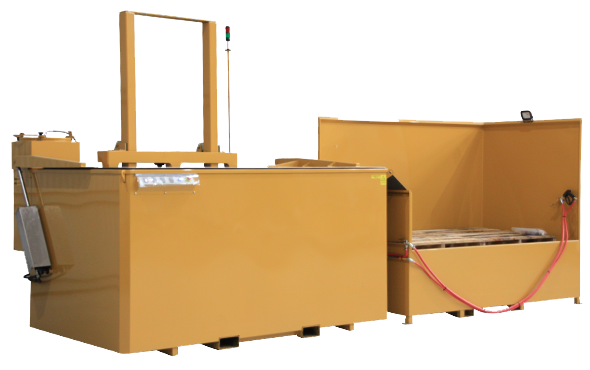
Various Names for Hot Tanks
Hot tanks, often referred to as hot wash tanks or caustic baths, are designed to clean engine parts and heavy-duty machinery by using heated water and detergents. These names highlight the high-temperature process and chemical cleaning capabilities.
Hot Tanks vs Sand Blasting
While sand blasting is abrasive and can cause surface damage, especially to delicate components, a hot tank offers a gentler yet thorough cleaning process, reducing the risk of wear or damage to parts while still effectively removing grime and contaminants.
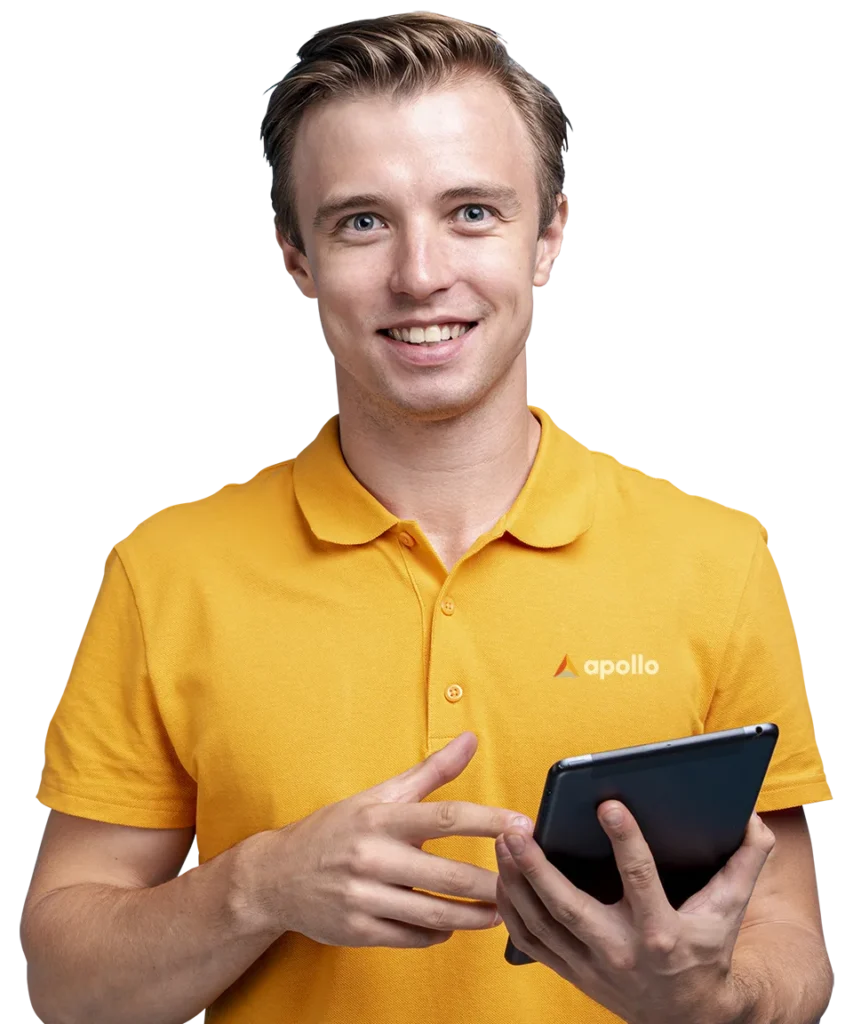
Contact us today
Learn how our cutting-edge parts washer machine can revolutionise your operations and contribute to a more efficient and sustainable future for your business.